 Bumpless Transfer PID Controller
Snapshot of the front panel of the simulator:
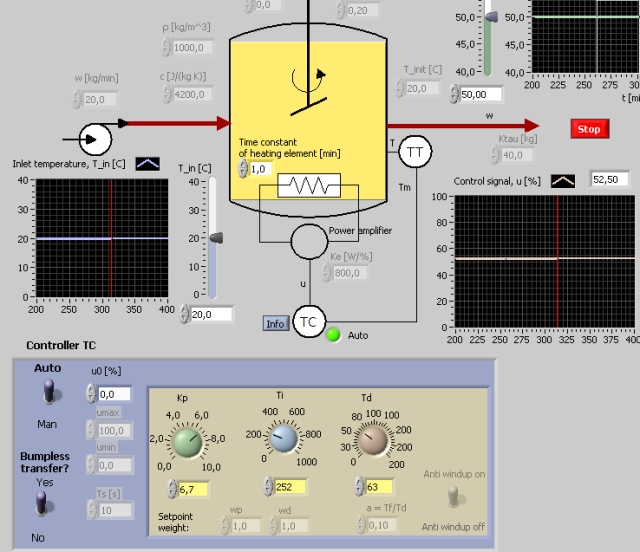
A temperature control system for a liquid (water) tank
with inflow and outflow is simulated. Via the front panel of the simulator
you can select whether the temperature controller has bumpless transfer
between automatic and manual mode or not. Bumpless transfer means that the
control signal is not changed abruptly at switching between automatic and
manual mode.
How is bumpless transfer realized in the PID controller used in this
simulator? The PID controller calculates the control signal as follows:
u = u0 + up + ui + ud
where u0 is the nominal control signal, which
is an adjustable constant. When the controller is in manual mode, u = u0.
- Bumpless transfer from automatic to manual mode is realized
by giving u0 value equal to the control signal immediately
before the switching (from automatic to manual mode).
- Bumpless transfer from automatic to manual mode is realized
by ensuring that u0 keeps its value from manual mode and that
up,
ui and ud are set equal to 0 immediately before
the switching.
If bumpless transfer is deactivated (which is an option in this
simulator), u0 maintains its value from automatic mode in
manual mode (thus it does not get the value of u as it is immediately
before the switch). Also at switching from manual to automatic mode,
u0 maintains its value (this is the same implementation as for
bumpless transfer)
Aim
The aim of this simulator is to demonstrate why it is important that a PID
controller has bumpless transfer.
Motivation
Bumpless transfer is an important property of practical PID controllers. You
can assume that bumpless transfer is implemented in commercial PID controllers.
If you are to implement a practical controller yourself, you should implement it
with bumpless transfer.
The normal operating point of the process is defined
as follows:
- The tank temperature T is 50 degrees C. The temperature setpoint TSP
is 50 deg C.
- The inlet temperature Tin is 20 deg C.
You can use the following PID settings (according to the
Ziegler-Nichols' closed loop method):
Kp = 6.7; Ti = 250min; Td
= 63 min
Unless otherwise stated the tasks below assumes that the simulator
runs.
- Control without bumpless
transfer:
- Set the controller in automatic mode. Deactivate bumpless
transfer using the proper switch in the parameter field of the PID
controller. To clearly demonstrate the drawback of not using bumpless
transfer you should set the nominal control value u0 to 0.
Let the temperature settle at the setpoint value (50
deg C) (the integral term in the controller ensures zero static control
error even if u0 if 0).
- Switch the controller from automatic to manual mode, which implies
that the control signal to the process is u0 = 0.
Characterize the control action during the mode switching.
- Switch the controller from manual to automatic mode, which implies
that the control signal is equal to the sum of u0 and the P-, I-
and D-terms. Characterize the control action during the mode switching.
- Control with bumpless transfer:
- Set the controller in automatic mode. Activate bumpless
transfer via the proper switch in the PID parameter field. You may set u0
to 0. Let the temperature settle at the setpoint value (50
deg C).
- Observe the value of u (it is assumed that the control error is
zero, cf. Task 2a). Switch the controller from automatic to manual mode.
Characterize the control action during the mode switching. Which value
did u0 get immediately after the switching (compare with the
value of u just before the switching)?
- Switch the controller from manual to automatic mode. Characterize
the control action during the mode switching.
[SimView] [TechTeach]
Updated 16 April 2017.
Developed by
Finn Haugen.
E-mail: finn@techteach.no. |