 Gain Scheduling
Snapshot of the front panel of the simulator:
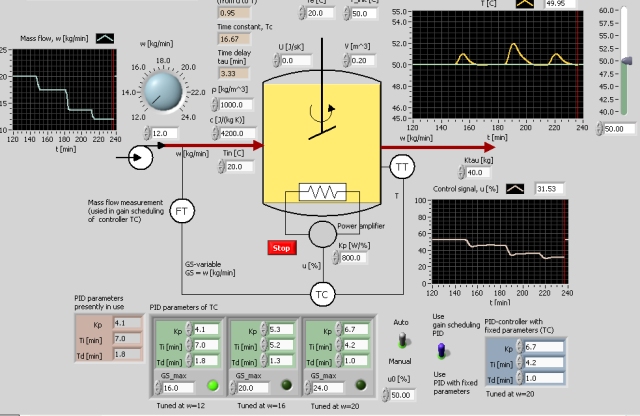
Description of the simulated system
A temperature control system of a heated stirred liquid tank with
continuous throughflow may vary, is simulated, see the front panel of the simulator.
It can be shown (see below) that the process dynamics (gain, time
constant, time delay) largely depends on the mass flow through the tank,
so the PID parameters should be be adjusted as functions of the mass flow
to maintain satisfactory dynamics (as good stability) of the control
system. In other words: Gain scheduling may be necessary.
About the process to be controlled
A process model can be derived from an energy balance (it
is for simplicity assumed that the heat transfer through the walls is
zero, i.e. U =
0, see the front panel of the simulator):
(1) d(crVT1)/dt = cw(Tin - T1) + P
where the power P [W] is given by
P = KP*u
where u [%] is the control signal.
T1 is the temperature of the liquid in the tank
assuming homogenous conditions. In practice there is a time delay
t in the response in the temperature sensor relative to an
excitation in the supplied power P. Thus,
(2) T(t) = T1(t-tau)
We assume that the time delay is inversely proportional to
the mass flow w:
(3)
tau = Ktau/w
The nominal operating point
The nominal operating point is charactericed as
follows:
- The tank temperature T is 50 degrees C,
- The inlet flow temperature Tin is 20 degrees C.
The controller
In the simulator the gain scheduling PID controller of the PID
Control Toolset in LabVIEW is used. In this controller a piecewise
constant interpolation is used between the different PID parameter sets.
In each interval the PID parameter values are held constant at a
conservative value, which implies that the stability is ensured during the
interval.
Aims
The aims of the tasks below are as follows:
- To demonstrate that the dynamics of a process may vary with process
parameter value, here: the mass flow through the system.
- To calculate proper PID settings for various mass flows, to be used
in a gain scheduled PID controller
- To observe the benefits of gain scheduling (i.e. an adaptive
controller) compared to a controller with fixed parameter values.
Motivation
Gain scheduling is an important practical way to implement an adaptive
PID controller, which means that the controller is continuously adapted to
the process it controls. Gain scheduling is available in many commercial
PID controllers.
A typical kind of processes which may require gain scheduling (i.e.
controller adaptivity) is processes with varying mass flow, as in the
present simulator. Concrete examples of such processes are heat exchangers
and continuous reactors being in a process line with varying production
rate.
- Varying process dynamics:
- From the model equations (1), (2) and (3) above, derive the transfer function
HP(s) from the control signal u [%] to the temperature T. This
transfer function becomes of first order with time delay. Show that the transfer
function has the following parameters:
(4) gain Ku = KP/(cw)
(5) time constant Tc = rV/w
(6) time delay
tau = Ktau/w
Thus, the process dynamics varies with the mass flow w.
- Run simulations to demonstrate that Ku, Tc and t
depends on the mass flow w as found in Task a above. Qualitative
resultes are sufficient (thus, you are not expected to calculate the
values of the gain, time constant and time delay for different values of
w). (Tips for
the simulations: Set the controller in manual mode. Change the
supplied power as a step from the value, P0 (found
experimentally, although you may calculate it from the model), which
keeps the process at the operating point, and observe the response in
the tank temperature.
- PID controller with fixed parameters:
- Controller tuning: Find
proper PID settings for w = 20 (using e.g. the Ziegler-Nichols'
closed loop method).
Alternatively you can use the parameter values shown on the front panel of the simulator.
- The dynamic behaviour of the control
system when the process dynamics varies: Reduce
the
mass flow w to its smallest value (12 kg/min). How does the process
parameters K, Tc and tau
vary (the
values are calculated and shown on the front panel of the simulator)?
Is the stability of the control system still satisfactory? Does it
seem to be need to adjust the PID settings as a function of w?
- Choosing mass flow for conservative
controller tuning: By
conservative controller tuning is meant that the control system is
guaranteed to not have bad stability.
Which value of the mass flow w should be chosen for conservative
controller tuning? (You do not have to run simulations to give an
answer..)
- Gain scheduling (adaptive) PID
controller:
- Controller tuning: Tune the PID
controller (using e.g. the Ziegler-Nichols' closed loop method) for
the following three w values: 16, 20 and 24 kg/min. Alternatively
you can use the PID settings shown on the the front panel of the simulator.
The above mentioned w values are used as the gain scheduling
parameter P, see the front panel of
the simulator.
- The dynamic behaviour of the control
system when the process dynamics varies: Use a gain
scheduling PID controller. First, set the mass flow w at its maximum
value, 24 kg/min, and let the controller system stabilize for this w
value. Then, reduce the w value to 12 kg/min. This reduction may be
in the form of three stepwise changes as follows: From 24 to 20, from
20 to 16, from 16 to 12). Observe that both the process parameters
and the controller parameters varies. Is the stability of the
control system satisfactory for any mass flow? Is gain sheduling
(adaptivity) beneficial compared to using a controller with fixed
settings, cf. Taks 2 above?
[SimView] [TechTeach]
Updated 19. January 2008.
Developed by
Finn Haugen.
E-mail: finn@techteach.no. |