 Multivariable Control Using Linear Decoupling
Snapshot of the front panel of the simulator:
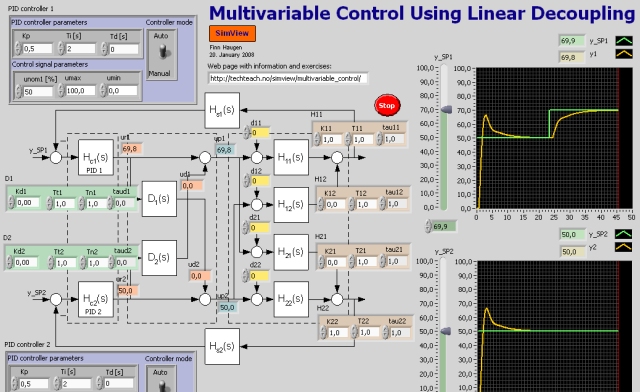
I this simulator a 2x2 multivariable system represented by a model
consisting of 4 transfer functions - one in each of the 4 couplings
between the 2 control variables and the 2 output variables. Each of the
transfer functions is a "first order with time delay":
yi(s)/uj(s) = Hij(s) = Kij(e-tijs)/[(Tijs
+ 1)]
The aims of this simulator is to give an understanding of the dynamics
of a multivariable process, to give experience with controller tuning, and
to observe the benefits of using decoupling.
Multivariable processes may be difficult to control due to cross
couplings in the process, which causes interaction between the control
loops. The PID controller tuning shoould follow certain procedures. Using
a decoupler between the PID controllers and the process may give better
control. Linear decouplers are available in some commercial control
systems.
- Configuring a process without cross
couplings:
- Choose parameter values of the process transfer functions (but
you may keep the default values),
but it is required in this subtask that the process has no
cross couplings.
- Verify the process dynamics (as expresses by the
transfer functions) by running some setp response tests (steps in
the control variables with the controllers in manual mode). In
particular, verify that there are no cross couplings in the process.
- Controlling a process which does not have
cross couplings:
- Tune the PID controllers.
- Show (using simulations) that there the control loops does not
interact.
- Single loop control of a process which has
cross couplings:
- Choose process parameters so that the process has cross
couplings (in both directions), e.g. K12 = K21 = 0.5, and time
delays equal to 0.5, and time constants equal to 1. Verify (using
simulations) that there are cross couplings in the process.
- Keep
the the PID settings from task 1.
- Verify (using simulations) that there are interactions
between the control loops.
- What happens to the stability of
the control system if the cross couplings becomes stronger (you
can increase the proper gains)? Adjust the PID parameters so
that the stability again is acceptable.
- Tune the PID controller using the following procedure:
(1)
Tune the controller in each of the loops in turn with all the
other controllers in manual mode. (2): Close all the loops (set
all controllers in automatic mode). (3) If there are stability
problems, reduce the gain and/or increase the integral time of
the controllers in the least important loops.
- Control based on decoupling:
Keep the process parameter values from Task 3 above.
- Find a decoupler for the process (calculate the parameters of
the transfer functions in the decoupler from the process model).
Show (using simulations) that the decoupling works (run step
response tests of the process, with the controllers in manual mode).
- Tune the PID controllers for the process including the decoupler.
Show (using simulations) that there is no interaction between the
control loops. (Note: You may observe a steady state control error
even though there is integral action on the controllers. This may
stem from saturation in the control signal as it tries to compensate
for the disturbance which the cross couplings represents.)
[SimView] [TechTeach]
Updated 2 September 2017.
Developed by
Finn Haugen.
E-mail: finn@techteach.no. |