 Speed Servo
Snapshot of parts of the front panel of the simulator:
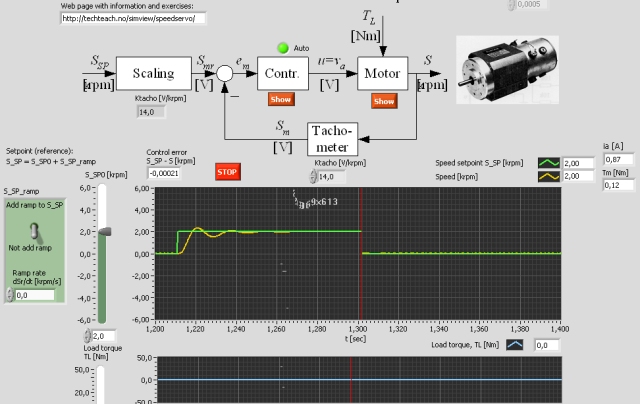
Description of the simulated system
A speed control system - i.e. a speed servo -- is simulated. The motor
is the DC motor Electro-Craft
S-19-3AT which is an armature controlled, voltage controlled DC motor.
The speed is measured using a tachometer.
The tachometer gain and the other motor parameters can be adjusted
from the front panel of the simulator.
Mathematical model
In the expressions below the following quantities are used: S is
rotational speed. va is armature voltage. ia is
armature current. Tf is friction torque. TL is
load torque. J is the sum of the intertias of the motor and the load, i.e. J = Jmotor +
Jload. B is the sum of the damping coefficients of motor and
load. La is the armature inductance. Ra is the
armature resistance. Ke is the voltage constant (the so called
back-emf constant). KT is the torque constant.
The values of the motor parameters can be adjusted from the front panel.
Dynamic model (differential equation)
A mathematical model of the motor can be found from the Kirchhoff's
voltage law on the armature circuit and the torque balance of the
mechanical rotation (refererence):
Kirchhoffs voltage law yields
(1) Ladia/dt = va - Raia
- KeS
Torque balance yields
(2) JdS/dt = KTia - BS - Tf - TL
Transfer function model
By taking the Laplace transform of the model above we will find the
following transfer function from armature voltage va to speed S:
(3) S(s)/va(s) = H(s) =
K/[(s/w0)2 + 2z(s/w0) + 1]
where the parameters are as follows:
Gain:
(4) K = Kt/(KtKe+BRa)
[rpm/V]
Relative damping factor:
(5) z =
0.5*(JRa+BLa)/[sqrt(JLa(KtKe+BRa))]
Undamped resonance frequency:
(6) w0 = sqrt[(KtKe+BRa)/(JLa)]
[rad/s]
Static model
By setting the derivatives in (1) and (2) equal to zero and eliminating
ia,
we get the following static model (all variables are assumed to have
constant values):
(7) S = [Kt/(KtKe+BRa)]va
- [Ra/(KtKe+BRa)](Tf
+ TL)
Aim
The aim of this simulator is to get a better understanding of how a
speed control system works dynamically.
Motivation
DC motors are used in many servo systems. Compared to other electro
motors DC motors are easy to model mathematically, and, hence, easy to
simulate.
In the tasks below is assumed - unless otherwise stated - that the process
(motor) is in its normal or nominal operating point, defined as
follows:
- The speed S is 3.0 krpm (revolutions per minute), which is used as
a nominal speed setpoint.
- The load torque TL is 0 Nm.
Unless other information is given, it is assumed that the simulator
runs while you do the tasks.
- Control using constant control signal.
Set the controller in manual mode.
- Find the nominal control signal u0 experimentally (on the
simulator) which brings the process to the nominal operating point.
- Change the load torque (disturbance) from 0 to -20 Nm. What is the
steady-state control error?
- Tuning a PID control:
In the subsequent tasks the motor speed is controlled by a PID
controller (unless otherwise stated). Adjust the controller using the Ziegler-Nichols'
closed loop method.
- Steady state setpoint
tracking and disturbance (load torque) compensation:
- Let the the load torque be zero and the speed setpoint 3.0 krpm.
What is the steady-state control error?
- Change the load torque as a step frm 0 to 20 Nm. What is the steady
state control error? Is there an improvement from task 1b?
- Are the static setpoint tracking and disturbance tracking perfect?
- Control using a P controller:
- Find a proper value of the controller gain.
- Are the static setpoint tracking and disturbance tracking perfect
with a P controller? (Simulate!)
- Tracking a setpoint ramp:
Let the load torque be constant. Let the setpoint be a ramp of slope 100
krpm/s.
- Use a PID controller. What is the steady state control error (as
read off from the front panel of the simulator)?
- Use a P controller. What is the steady state control error?
- The stability of the control system at parameter
changes:
Let the setpoint be 3.0 krpm and the load torque 0 Nm. Observe what
happen to the control system stability at the parameter changes
described below. In each task/experimentyou can excite the control
system via a small step in the setpoint. The experiments should be
performed independently, i.e. the parameter values should be reset to
default values once each of the experiments is finished.
- The control gain is increased (much).
- The integral time is
decreased (much).
- The derivative time is increased (much).
-
The tachometer gain (measurment gain) is increased (much).
- First, set the total damping coefficient B to zero. Then, reduce
the intertia of the load (much). Try to explain the influence that
this reduction has on the stability of the control system from Eq.
5.
[SimView] [TechTeach]
Updated 30. May 2008.
Developed by
Finn Haugen.
E-mail: finn@techteach.no. |